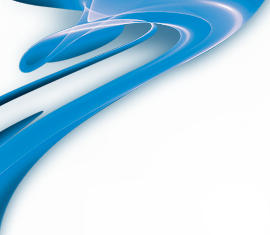
FREQUENTLY ASKED QUESTIONS (FAQ)
SUPER SEAL ADVANCED™ & TOTAL™
1. Are SUPER SEAL Advanced™, SUPER SEAL Total™ compatible with all oils and refrigerants, including 410a?
Yes, SUPER SEAL™ is packaged in a vacuum and uses the system’s refrigerant to charge the can and propel the sealant into the system. Use as per application guidelines below:
2. What size hole and pressures will SUPER SEAL™ repair?
For optimum success a system should not be leaking more than 15% of its total refrigerant charge over a 4 week period. SUPER SEAL™ has been specifically designed to seal micro pores, 300 micron (characterized as champagne leaks) and smaller, typical seasonal leaks. The repair by the sealant will withhold 800 psi, as well as, low pressure vacuum testing used in triple evacuation procedures. Note: SUPER SEAL™ cannot permanently seal cracks that are subjected to thermal expansion and contraction movement.
3. When should SUPER SEAL™ be used?
It should be used when conventional leak detection methods are unsuccessful and all attempts to find and fix a leak have been exhausted. Use in compliance with the Montreal Protocol & regional or federal laws for handling of refrigerant.
4. How does SUPER SEAL™ work?
SUPER SEAL™ is a light or low viscosity particle free liquid, the sealant is injected as a mist directly into the refrigerant stream utilizing our patented 29,000th of an inch orifice. As it travels with the refrigerant and oil throughout the system, the sealant exits the leak point and reacts with moisture in the atmosphere it forms a low tensile crystalline structure creating a permanent seal.
5. What if there is moisture in the system?
The addition of DRY R™ to all our Super Seal formulas adds an extra level of protection beyond what normal sealants can offer. The active ingredient in DRY R™ reacts with water to eliminate 20 drops of moisture from the system.
Higher levels of moisture can prematurely activate the sealant and cause formation at areas of moisture concentration such as driers, and metering devices, resulting in possible restriction and system failure. We recommend that technicians always adhere to ARI recommended levels of moisture for AC/R systems.
6. Will SUPER SEAL™ clog the valve core as I inject the product into the system?
No, when the sealant is injected into the system, it has already been combined with the refrigerant charge and the refrigerant acts as a solvent, cleaning the valve core as it passes through.
7. Will the sealant harm the compressor or any other components in the system?
No, the sealant is completely compatible with the electrical windings of the compressor motor. It will not interfere with compressor valves or form wax in cap tubes, orifices, or thermostatic expansion valves, and does not impede the lubricity of the system oil in any way.
8. What happens to SUPER SEAL™ while it is in the system?
The chemical formulation remains in a stable state while it travels within the dry refrigerant/oil stream. Only when it exits at a leak point and makes contact with moisture in the air does it begin to form a permanent seal.
9. How long will SUPER SEAL™ remain in the system?
It will remain in an active form for up to 10 years or longer protecting the system against micro leaks. As with any chemical mixture it will eventually break down into non active by-products which are safe and compatible to components, oil, and refrigerant and will not affect systems performance.
10. What happens if a line bursts on a system containing SUPER SEAL™?
Along with the refrigerant and oil, approximately ninety five percent of the sealant is carried out of the system. The remaining five percent of sealant will remain in the oil sump and condenser in a stable soluble oil state as a non reactive.
11. What happens to SUPER SEAL™ if I need to reclaim the refrigerant?
It is removed from the A/C or refrigeration system with the refrigerant and carried through the recovery machine to the recovery tank. Any repairs to the system are carried out using standard methods you would typically use on a unit, such as cleaning brazing points and using nitrogen when brazing.
12. How do I classify recovered refrigerant from a system which had SUPER SEAL™?
As long as the system did not experience a burn out or a compilation of mixed refrigerants, the recovered refrigerant needs only to be identified as used when returned to a refrigerant recycling depot. Cliplight sealants are vacuum packed, particle free and contain no propellants such as propane or isobutane and will not contaminate refrigerants. The sealant is a liquid and is easily separated with the oil during the recovering process.
13. Has the chemical technology in SUPER SEAL™ ever been used before?
Yes, the sealant technology in SUPER SEAL™ has been used for decades to seal leaks in underground gas transmission lines, as well as in pipes, tanks, compressors and gas pressurized vessels
14. Are there any checks to be completed before installing Super Seal™?
Yes, verify the system temperature readings: the temperature at the compressor base should not be in excess of 130°F/54°C , compressor discharge temperature above 225°F/107.2°C or a 2 degree or greater temperature differential across the liquid line drier. Should these conditions exist you must treat the system as contaminated with particulate and proceed accordingly.
DRY R™
1. What is in DRY R™? Why and how does it work?
The active ingredient in DRY R™ is referred to as a hydrolytic. DRY R™ eliminates moisture from the system by chemically disassembling the H2O molecule and reorganizing it into two new stable products. No particulates, gels, or polymers are formed. By eliminating moisture, DRY R™ allows the oil to continue to condition and stabilize the refrigeration system. DRY R™ does not mask water by raising the freezing point as in the case with alcohol products used in glycol mixtures.
2. When should DRY R™ be used?
DRY R™ should be used every time a system is opened up for repairs or when you suspect there is moisture in a system because of mechanical malfunctions or breakdowns. DRY R™ is especially suited for eliminating moisture content in all oils. DRY R™ can eliminate the need to change out the receiver dryer, and accumulator which may be contaminated with high moisture levels before the injection of Cliplight Super Seal Advanced.
3. Is DRY R™ able to remove blockages?
DRY R™ has been proven to effectively breakdown blockages and varnish films on moving parts such as TXV’s caused by moisture laden particulate.
4. Is DRY R™ compatible with all oils and refrigerants, including 410a?
Yes, DRY R™ is packaged in a vacuum and uses the system’s refrigerant to charge the can and propel it into the system.
5. How will DRY R™ affect liquid line dryers and metering devices?
The chemical nature and fast acting reaction of the product will eliminate system moisture quickly allowing the liquid line drier, receiver drier, or accumulator to accomplish a greater amount of work. Excess moisture from the drier will also be eliminated which will allow more room for additional moisture reclamation during operations. This in turn will prevent ice crystal formation at the orifice tube or expansion valve, allowing free flow of refrigerant.
6. Will DRY R™ harm my manifold gauge set or recovery equipment?
No, DRY R™ has non aggressive properties and is completely stable. While recovering refrigerant with DRY R™ the product passes through the gauges and recovery machine on to the recovery tank. During this operation it helps to remove residual moisture present in the gauge, machine and internal dryers.
7. Will DRY R™ improve the performance of Cliplight’s sealants and UV dyes?
Yes, the performance of both the sealants and the UV dyes are greatly enhanced because of the elimination of moisture from the system. The absence of moisture allows the sealants and dyes to remain soluble and miscible with the refrigerant and oil, retaining more energy to do more work when it arrives at the point of leakage.
8. How long will it remain active in the system?
It will remain active, eliminating moisture, until the system is opened up again for repairs or if a major loss of refrigerant and oil occurs.